Chemicals Risk Assessment
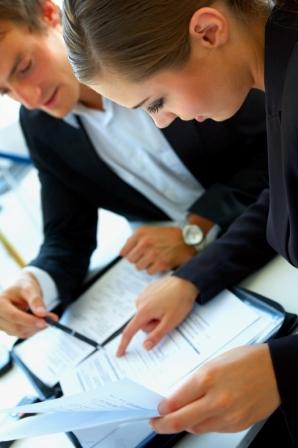
Almost all workplaces use chemicals which mean employees can be routinely exposed to paints, sprays, inks, toners and adhesives not to mention a wide range of materials used in cleaning and maintenance such as detergents and oils. Chemicals can be solids (e.g. dusts, fibres), liquids or mists (e.g. bleach) or gases / vapours (e.g. carbon monoxide, chlorine or ammonia). They can be individual substances like petrol or mixtures / products (e.g. paints, degreasers, ink and toners). Any chemical, in either gas, liquid or solid form, that has the potential to cause harm is referred to as a hazardous chemical. Chemicals include those that are brought into the workplace and used for processing (e.g. solvents and cleaning agents) and those that are generated by a process or work activity (such as fumes from welding / soldering) or generated as waste or residue (such as carbon monoxide from engine or exhausts).
How can chemicals cause harm to health?
Chemicals can cause harm to health ranging from mild skin irritation to cancer when they come in contact with the human body. The effects of hazardous chemicals may be seen immediately after contact e.g. chemical burn, or many years after contact e.g. lung cancer following exposure to asbestos. Harm can also occur following a single short exposure such as the use of a chemical for a couple of hours or longer-term exposures from the daily use of a chemical. Chemicals can come in contact with or enter the human body through inhalation (breathing in contaminated air), skin contact (splash, absorption through the skin), ingestion (swallowed accidentally e.g. not washing hands before eating) or injection (from sharp objects such as needles).
Examples of the effects of hazardous chemicals include:
- Skin irritation, dermatitis or skin cancer from frequent contact with oils
- Injuries to hands and eyes from contact with corrosive liquids such as acids / bases
- Asthma due to sensitisation to isocyanates in paints and adhesives
- Lung diseases following exposure to dusty environments such as respirable dust, wood dust or flour dust
- Death or injury from exposure to toxic gas, e.g. chlorine, ammonia, carbon monoxide
Some chemicals also present physical hazards such as the potential to ignite or support combustion of other chemical substances (an oxidiser).
Assessing the risk of chemicals
The Chemical Agent Regulations 2001 to 2021 point out the specific requirements necessary to complete a Chemical Agents risk assessment of the chemical agents used in the workplace. A generic assessment is unlikely to meet the requirements of the legislation. The Control of Substances Hazardous to Health (COSHH) Regulations are UK Regulations and do not apply in Ireland. COSHH assessments are UK requirements and do not meet the Irish legal requirements for risk assessments.
In the case of a new activity involving hazardous chemical agents, work shall not commence until after an assessment of the risk of that activity has been made and the preventive measures identified in the risk assessment have been implemented.
The risk assessments should be based on activities involving chemicals - the risk depends not only on the chemical or chemicals (many activities involve more than one) but also on how it is being stored, transported, used, generated or disposed of.
1. Make a list (inventory)
Walk around your workplace, check your purchase orders and make a list of all the chemicals you bring in and those generated by work activities or waste (welding fume, dust, residues).
Organise the list by job roles / activities. Many jobs involve more than one chemical so employees can be exposed to several hazards. Where there is exposure to several chemical agents, the risk shall be assessed on the basis of the risk presented by all such chemical agents in combination.
2. Identify chemical hazards
The most important sources of information on the hazards of the chemicals brought into your workplace are the label and safety data sheet (SDS). All chemical containers should be supplied with a label which clearly identifies the chemical and its hazards. Where a chemical is hazardous, the label should contain a signal word (danger or warning) and may include an associated pictogram and a hazard statement giving more detailed information on the hazard (e.g. causes serious eye irritation, causes skin irritation). It should also contain precautionary statements giving advice on safety precautions to be taken (e.g. keep out of reach of children, wear protective gloves / protective clothing / eye protection / face protection). Additional precautionary information may be provided in the safety data sheet. The safety data sheet is a document that should be provided by the supplier with all hazardous chemicals. The safety data sheet is a key tool for risk assessment as it includes detailed hazard information, advice on safe handling, use and storage, and the emergency measures to be followed in case of an accident.
For chemicals generated by work activities, you can get information from:
- HSA Website (e.g. RCS, Welding fumes)
- Professional organizations e.g. IOSH, BOHS
- Recognized Trade or representative Organizations
3. Assess exposure
Once you have identified your chemical hazards you then need to assess what the potential exposure is to your employees. This involves looking at each chemical which you have identified as hazardous and considering the following questions:
- How is the chemical used (e.g. sprayed, poured) and how often is the chemical used?
- How will the user be exposed? (e.g. breathing it in, contact with skin?)
- How much is used /generated ?
- How long is each user exposed to the chemical? (e.g. full shift or a few minutes?)
- Who uses the chemical? (e.g. how many people?)
- Are any vulnerable groups potentially exposed? For example, identify if reprotoxins are in use.
- Is the chemical mixed with other chemicals or exposed to high temperatures or pressure?
- Can non-users be exposed? (e.g. people working nearby, visitors, cleaning or maintenance staff?)
4. Control your chemical risks
Once you have assessed the risk associated with your chemicals, control measures must be put in place in order to keep your employees, your workplace, and the environment safe.
You should first consider if you can eliminate the hazard by changing the process or removing the hazardous chemical.
If you cannot eliminate the chemical(s), can you substitute the hazardous chemical with another, non-hazardous or less hazardous chemical? For example, you could replace isocyanate based paints with water based paints or you could use a less hazardous form of the same chemical (e.g. using a pellet rather than a powder form of the chemical could have a significant effect on reducing inhalable dust levels).
Where the above options are not possible, exposure to hazardous chemicals should be minimised and additional control measures must be put in place to remove or reduce the risks to employees:
- Engineering controls e.g. local exhaust ventilation (LEV), on tool extraction, isolation / containment hoods or booths
- Review of current work practices or procedures to reduce the frequency and length of exposure
- Training for employees on the chemicals currently used in the workplace, what the chemical hazards are and the potential risks to their health, and how to handle chemicals safely
- Hygiene arrangements e.g. separate meal and wash facilities, designated smoking areas or a no smoking policy
- Specific Storage arrangements so that chemicals are stored correctly, safely and securely. (Information on storage is available in section 7 of the SDS)
- Personal protective equipment (PPE), e.g. eye protection, gloves, masks and respiratory masks (RPE). As these are the last line of defence, PPE is used to control any residual risk after taking all the other measures. PPE only protects the user. Information on the correct PPE and RPE is provided in section 8 of the SDS, but contact the supplier if unclear (Specify in your risk assessment the exact glove type, filter type etc.)
- A good level of housekeeping
- Correct disposal of waste
- Emergency procedures in case of an accident, incident or spillage, e.g. eyewashes, showers, spill kits
5. Record and review
Write down your findings (this can be part of a work instructions) and discuss them with your employees. Consultation with your employees is necessary at every step and especially when implementing the findings of your chemicals risk assessment.
You may need to draw up an action plan, detailing who is responsible, for what action and when will it be carried out.
As no workplace remains the same, review your risk assessment at least once per year, and update if necessary. When changes such as new employees, machinery, equipment or materials occur in the workplace it is necessary to review the risk assessment. Change in work patterns such as overtime or shift work, the needs of pregnant/nursing employees and those with special needs must also be included.
Advice on Completing Chemical Risk Assessments
The following are examples of assessments that Inspectors have seen during inspections and investigations. They are in different formats because different formats suit different types of activities involving chemicals. The examples are varied as chemicals are varied. An approach/template/format that works in one situation will not work in another.
The formats presented below have been reviewed and comments included on how they should be improved. They illustrate how you can improve the compliance of your risk assessments. These are for interactive use and not for printing. If you print these then the pop-up directions disappear and the documents are invalid.
Example 1
Example 2
Example 3
Example 4
Quick Start questionnaire
Find and reduce the safety and health hazards associated with dangerous substances and chemical products in workplaces within your company - See EU OSHA Dangerous Substances e-tool (available in several languages).
This information sheet gives employers and employees practical advice on how to assess the risks from the chemicals in their workplace and how to manage chemicals safely.