Clearing Blocked Crushers
This guidance cannot cover every risk and is not comprehensive. It does not attempt to detail individual machinery safety concerns, but will only highlight those key matters of concern. Crushing is the first step in converting rock into usable products. Essentially, crushing is no more than taking large rocks and reducing them to small pieces. Crushing is sometimes continued until only fines remain. Blockage incidents can be greatly reduced by supplying rock that is properly sized to match the primary jaw opening. Prevention of oversize in feed material starts at the face with good fragmentation. Removal of oversize material before delivery to the plant and vigilant control of the crusher feeder will make blockages unlikely. | 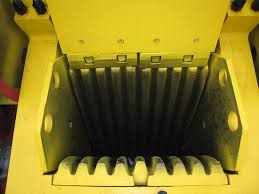 |
At some operations, all the crushing is accomplished in one step, by a primary crusher. At other operations, crushing is done in two or three steps, with a primary crusher that is followed by a secondary crusher, and sometimes a tertiary crusher.
Raw material of various sizes are brought to the primary crusher by rear-dump haul units, or carried by a wheel front-end loader. Primary crushing reduces excavated rock to a more manageable size. There are different types of primary secondary and tertiary crushers including jaw crushers, gyratory crushers, impact crushers, and autogenous crushers.
Crushers remain a potential serious risk to persons even when the equipment has been de-energised and isolated because a release of a blockage can release a huge amount of stored energy. Tramp metal is a common cause of blockages and can often expose people to risk during clearance operations, the sudden, uncontrolled release of energy can release a lethal projectile amongst men working on the task.
Blockages should be cleared from a position of safety and should not involve any one entering or being lowered into the crushing area. Hydraulic breakers are often added to jaw and other crusher installations so that they can be operated from a safe position, often in the control cabin using CCTV, other operations use a back hoe loader with a hammer tool or an excavator to free blockages and in older installations a pry bar and/or hammer can be used, pry bars should never be used on or near a crusher while it is running. Before any barring begins, the plant should be shut down and locked out.
Whichever method is used there should be clear procedures in place that are followed and personnel should not enter the area of the blockage unless the stored energy has been released and precautions should be in place so that the sudden release of the blocked material does not place persons at risk of injury. Occasionally personnel may need to enter the blockage area to place lifting chains or straps on the oversize rock so that it can be lifted out and in such circumstances the crusher plant must be isolated and kinetic energy released (where possible), personnel must move to a position of safety before lifting takes place .
Action when a crusher becomes blocked
- Have a nominated person supervise the activity and call for assistance as necessary
- Stop the feed to the crusher at the earliest opportunity
- Remove excess material by mechanical means where possible before the cause of the blockage can be dealt within where an amount of removal by hand is necessary the crusher and associated plant must be stopped and isolated
- Manual removal should only be carried out by suitably trained and competent persons
Crusher Types
Jaw Crushers
Jaw crushers operate by squeezing rock between two surfaces, one of which opens and closes like a jaw. Rock enters the jaw crusher from the top. Pieces of rock, that are larger than the opening at the bottom of the jaw, lodge between the two metal plates of the jaw. The opening and closing action of the movable jaw against the fixed jaw continues to reduce the size of lodged pieces of rock until the pieces are small enough to fall through the opening at the bottom of the jaw.
Gyratory Crusher
A gyratory crusher breaks rock by squeezing the rock between an eccentrically gyrating spindle, which is covered by a wear resistant mantle, and the enclosing concave hopper. As oversize rock enters the top of the gyratory crusher, it becomes wedged and squeezed between the mantle and hopper. Large pieces of rock are broken once, and then fall to a lower position (because they are now smaller) where they are broken again. This process continues until the pieces are small enough to fall through the narrow opening at the bottom of the crusher.
Impact Crusher
Impact crushers, which are also called hammer mills, break rock by impacting the rock with hammers that swing on a rotating shaft. The practical use of impact crushers is limited to soft materials, such as phosphate, gypsum, weathered shale’s, etc. Impact crushers cannot handle as large a top sized material as jaw, or gyratory, crushers can; however, impact crushers can make a finer sized product.
Autogenous Crusher
In recent years, autogenous crushers have been adapted for crushing excavated rock in primary crushing circuits. Consequently, autogenous mills have increased in importance as a means of crushing and grinding. In autogenous crushers, the rock to be crushed also provides the crushing force. Crushing is accomplished by the tumbling action of the rock. Flexible crushing circuits can be constructed so that hard and soft rock, can be processed. Wet, sticky materials can also be processed in autogenous mills, while the same ore would present difficulties for other types of crushers.