Ventilation and Indoor Air Quality
Introduction
Workers spend a significant amount of time indoors, and the quality of air within indoor work environments has a direct impact on the health, well-being and productivity of those workers.
Contributing factors to poor indoor air quality (IAQ) include inadequate or poor ventilation. poor external air quality and exposure to a range of chemicals, biological agents and other contaminants in the workplace air. Poor IAQ can cause a variety of both short-term and long-term health problems.
Ventilation is a critical method of removing contaminants from buildings and is essential to ensuring good indoor air quality (IAQ) as well as thermal comfort.
Ventilation refers to the movement of outdoor air into a building, and the circulation of that air within the building or room while removing stale air to improve the air quality. This can be achieved through natural means or by mechanical means or both.
Types of Ventilation
Natural Ventilation is the way that outside air can be brought into a building without using fans or other mechanical means. This includes airflow through openings in the building such as windows, doors, roof turrets and other vents.
Mechanical ventilation describes the means of bringing air into and /or out of a building using powered means e.g. fans. Depending on the source of outside air, it may need to be filtered or cleaned before it enters the building. The principle of supply and extraction is that one series of ducts and inlet grilles brings outside air into a space, while another set of ducts extracts the stale air and exhausts it outside. Incoming air can be located in diffusers in the ceiling, on the wall or on the floor.
Heating, ventilation and air conditioning systems (HVAC) are a combination of both mechanical ventilation and air conditioning. Recirculation of untreated air should be avoided. Air conditioning alone does not provide fresh air or ventilation but it controls the air temperature and/or controls humidity and recirculates the air.
Local exhaust ventilation (LEV) is an engineering system designed to capture contaminants (dust, mist, fume, vapour, gas) in the workplace at source and transport them to a safe emission point or to a filter/scrubber. It is not part of general ventilation. Please refer to specific LEV guidance for employers here.
Relevant Legislation
The Safety, Health and Welfare at Work (General Application) Regulations 2007, as amended by S.I.255 of 2023, require employers to make sure sufficient fresh air is provided in enclosed places of work.
This can be achieved by:
- natural ventilation which relies on passive air flow through windows, doors and air vents that can be fully or partially opened.
- mechanical ventilation using fans and ducts including window fans to bring in fresh air from outside.
- a combination of natural and mechanical ventilation, for example where mechanical ventilation relies on natural ventilation to maximise fresh air.
Where present, mechanical ventilation systems must be maintained in good working order e.g. as part of a plant maintenance system, and operate in such a way that employees are not exposed to draughts which cause discomfort. Mechanical ventilation systems must also be cleaned regularly to avoid contamination.
Ventilation arrangements or planned changes to ventilation need to also consider in addition to health and safety regulations the regulatory requirements under building and food along with other consequences such as comfort, cost, energy use, noise and security.
Assessing Ventilation in the Workplace
Ventilation of enclosed workplaces should be considered as part of workplace risk assessments. As part of a risk assessment, workspaces that are occupied and are poorly ventilated should be identified.
Such as:
- Areas where people work and where there is no mechanical ventilation or natural ventilation such as open windows, doors or vents etc.
- Areas that use mechanical ventilation if the system recirculates air and has no outdoor air supply in place.
- Areas that are stuffy or smell bad.
Workplaces with multiple or complex ventilation systems in place, may require expert advice.
Use of Carbon Dioxide (CO2) Monitors as a Proxy to Identify Poorly Ventilated Areas
Carbon Dioxide (CO2) Monitors can be useful way of checking for poorly ventilated areas where people work. CO2 concentrations above 1400 ppm are likely to be indicative of poor ventilation and the HAS Code of Practice for Indoor Air Quality recommends maintaining CO2 concentrations below 1000 ppm for adequate ventilation. Outdoor air concentrations of CO2 are approximately 400 - 480 parts per million (ppm). Where there are high CO2 concentration levels or the levels are increasing upwards towards the indicative values of poor ventilation, then it is recommended that mitigation measures to either increase ventilation or adjust occupancy are taken.
CO2 monitors are however less effective in work areas used by few people or in large workspaces, nor are they recommended where there are other CO2 sources than people, such as fuel combustion (fires and stoves) and cooking.
CO2 monitors should be
- CE marked
- based on non-dispersive infrared (NDIR) technology
- have a measurement range up to at least 2,000 ppm
- used in accordance with the manufacturer’s instructions.
How to improve ventilation
While ventilation requirements cannot easily be distilled into one simple approach that everyone can follow. Measures need to be specific to the setting, taking into account the nature of the building and users, ventilation type, length of exposure and work activities being undertaken. There are however practical ways to improve your ventilation.
Natural ventilation can be improved by:
- opening doors, windows and vents wherever possible especially between uses/users to increase the amount of fresh air without impacting workers comfort, ,
- avoid closing doors or windows completely when people are in a naturally ventilated area.
- “air rooms” as frequently as possible. This may be best done when the room is unoccupied and at the beginning and end of the day or when during breaks.
- Opening windows / doors / vents, particularly those opposite each other, will facilitate a quick exchange of room air for fresh air.
Note: Fire doors should not be propped open unless fitted with approved automatic closers so that they function as fire doors in the event of an alarm or fire.
Mechanical ventilation
- Ensure the mechanical system is used correctly and operating efficiently as per its
Design. It is important to make sure that mechanical ventilation systems and /or extractor fans are used correctly. If unsure, contact the manufacturer or service engineer
- Set the system to maximise fresh air and avoid recirculation.
- Ensure the mechanical ventilation system is regularly maintained, as per the manufacturer’s instructions, by a trained and competent person. Correct filters should be used in line with the manufacturer’s specifications and air filters should be properly sized and within the recommended service life.
- Extend the operating times of mechanical ventilation systems to before and after people use work areas.
- The system should be optimised to maximise the air changes / fresh air intake i.e. the amount of fresh air should be maximised and the recirculation minimised, as far as systems allow. Do not adjust mechanical settings without expert advice.
- Recirculation of air should be avoided where possible or the air may need to be filtered (e.g. through a HEPA filter).
- Ensure extractor fans in toilets and bathrooms are functional and running when in use or even continuously. Ensure that such fans are not recirculating air to other poorly ventilated areas of the workplace where workers are exposed
- Don't lower mechanical ventilation rates if the number of people in an area reduces temporarily
Where temperature is a concern,
- Open windows and doors fully to air spaces before and after occupancy e.g. open windows fully at start and end of the day to ventilate the room fully.
- Partially opened windows and doors, partially opened windows and doors can still provide adequate ventilation especially when weather is colder.
- Opening higher-level windows to create fewer draughts
- Set heating to maintain a comfortable temperature or consider if additional sources of local heating are required. (Only use fan convector heaters if the area is well ventilated.)
Air cleaning and filtration units /Other Equipment and Systems
Local air cleaning is not a substitute for good ventilation. It may be beneficial in reducing risks in some spaces, particularly where it is not possible to increase ventilation using natural or mechanical means as set out above. The most suitable types to use are those with high efficiency particulate air (HEPA filter]. You should prioritise any areas identified as poorly ventilated for improvement in other ways before you think about using an air-cleaning device.
These devices are usually stand-alone and can be deployed in any space or installed in a manner similar to a local air conditioning unit. While these devices can increase the airflow, their effectiveness will depend on the volume of the room/area and the flow rate through the device. Two smaller devices at different locations may be more effective than 1 large device. Therefore, it is important that if considering this as an option the device should be of a suitable specification for the relevant area. Their introduction and use in the workplace should be done as part of an overall assessment of the existing ventilation systems in place to show that their use is necessary. There are also drawbacks in using these devices and these impacts need to be risk assessed before using them. In addition, operators need to be trained to use and maintain them. They should not be placed beside windows or barriers.
When comparing devices, check that the performance ratings are comparable e.g. do they specify a decay rate e.g. cleaning room after occupancy or a rate for continuous occupancy of the space. Where noise is a potential issue, running the device at less than full power can reduce noise. However, additional devices may then be required.
Other devices such as ozone generating devices and air disinfection devices may present additional physical or chemical related hazards in the workplace and their use should be fully justified by an appropriate risk assessment. They tend to be best suited to more specialist applications and settings and require competent advice from qualified personnel prior to their installation. It is not recommended to use these devices in occupied spaces.
Code of Practice for Indoor Air Quality
A Code of Practice for Indoor Air Quality is now available to assist employers with managing IAQ in their workplaces. The Code aims to provide practical guidance on:
- improving IAQ;
- improving ventilation in workplaces;
- establishing a set of acceptable values for specific chemical and physical parameters; and
- describing mechanisms to identify, evaluate and control IAQ issues.
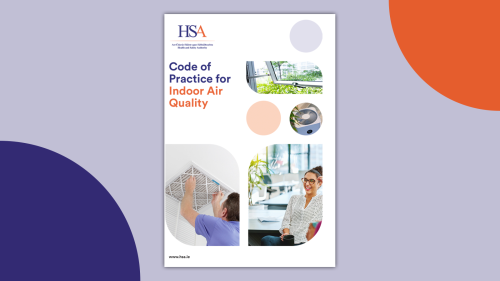
Further information/Resources
Further information on ventilation is available at:
- HSA Code of Practice for Indoor Air Quality
- HSA Guide to the Safety, Health and Welfare at Work (General Application) Regulations 2007, S.I. No. 299 of 2007
- NSAI - Irish Standard I.S. EN 16798-1:2019 Energy performance of buildings - ventilation for buildings. Available from www.nsai.ie
- Chartered institution of building services engineers www.cibse.ie