Fire Prevention
The safest way to deal with fire is to prevent it.
Under Section 19 of the Safety, Health and Welfare at Work Act 2005 (the 2005 Act) every employer shall identify hazards, assess risks and have a written risk assessment, including any unusual or other risks. To comply with Section 19, employers are required to carry out risk assessments and to record these in the Safety Statement. A fire safety risk assessment should be conducted. Fire prevention should form part of this.
A fire safety risk assessment should include
Back to top
Fire Prevention
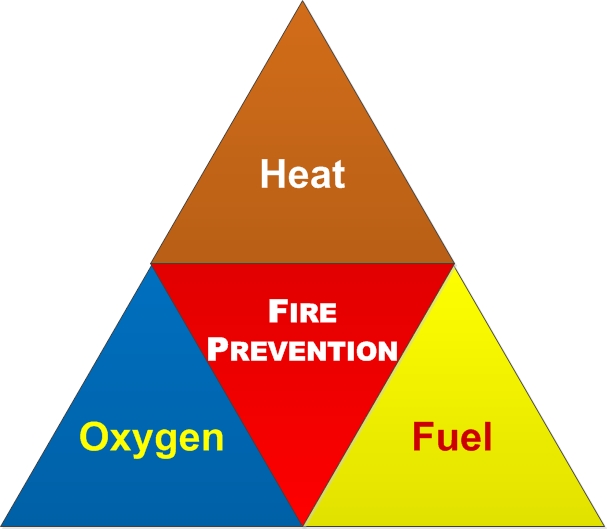 | The Fire Prevention Triangle - Heat, Oxygen and Fuel A fire needs three elements - heat, oxygen and fuel. Without heat, oxygen and fuel a fire will not start or spread. A key strategy to prevent fire is to remove one or more of heat, oxygen or fuel. The risk assessment should include detail on all three elements to minimise the risk of a fire starting/ spreading. |
A fire prevention strategy and a fire risk assessment should include detail and a full consideration of all of the issues - including issues arising from heat, oxygen and fuel. Advice on these three elements follows. This advice is not exhaustive and is given in no particular order.
Back to top
Heat
Heat can be generated by work processes and is an essential part of some processes such as cooking. This heat must be controlled and kept away from fuel unless carefully controlled. Heat generated as a by-product of a process must be dealt with properly.
Back to top
Heat Safeguards
Back to top
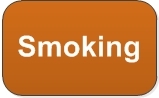 | Smoking |
- Provide no-smoking signs at appropriate locations
- Ensure smoking area(s) are away from flammable materials
- Arrange for cigarettes and matches to be disposed of safely and away from other combustible rubbish
| 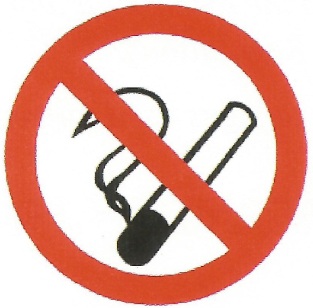 |
Back to top
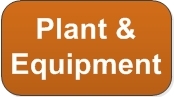 | Plant and Equipment |
Plant and equipment which is not properly maintained can cause fires.
- Ensure all work equipment protects against catching fire or overheating
- Ensure proper housekeeping, such as preventing ventilation points on machinery becoming clogged with dust or other materials - causing overheating
- Have electrical equipment serviced regularly by a competent person to prevent sparks and fires
- Properly clean and maintain heat producing equipment such as burners, heat exchangers, boilers (inspected and tested yearly), ovens, stoves, and fryers. Require storage of flammables away from this equipment.
- Use a planned maintenance programme to properly maintain plant and equipment. Review your programme if you already have one.
- A planned maintenance programme should deal with
- frictional heat (caused by loose drive belts, bearings which are not properly lubricated or other moving parts)
- electrical malfunction
- flammable materials used in contact with hot surfaces
- leaking valves or flanges which allow seepage of flammable liquids or gases
- static sparks (perhaps due to inadequate electrical earthing)
Portable Heaters
- Do not use portable heaters unnecessarily.
- They should have emergency tip-over switches, and thermostatic limiting controls.
- Turn them off if people leave the room or are going to sleep
- Ensure they are 1M away from anything that can burn
- Do not use them to dry clothes
Back to top
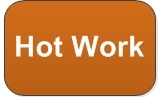 | Hot Work |
Hot work often arises from construction and/ or maintenance activities. Hot work is work that might generate sufficient heat, sparks or flame to cause a fire. Hot work includes welding, flame cutting, soldering, brazing, grinding and other equipment incorporating a flame, e.g. tar boilers, etc. Hot work can be very dangerous and stringent controls must be in place. | 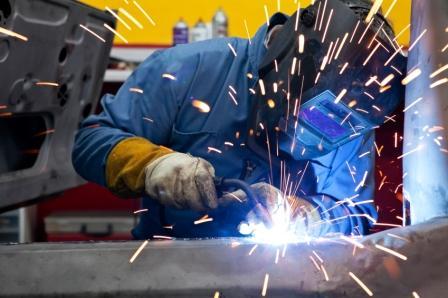 |
- Identify all hot work
- Only allow hot work if no satisfactory alternative
- Ensure relevant contractors are aware of hot work procedures and controls
- Use a hot work permit system including
- fire-resistant protective clothing
- clear responsibility
- logging and audit processes
- routine checking and supervision
- item to be worked on removed to safe area
- remove or protect combustible or flammable materials
- prevent, suppress and control sparks
- prevent, suppress and control heat
- provision of and training on suitable fire-fighting equipment
- provision of a separate person to fire-watch and use fire-fighting equipment – the fire watcher
- particular precautions for special risks, e.g. confined space
- leave workplace clean and safe
- final check of area at least 60 minutes after completed job and certainly prior to premises being vacated
Back to top
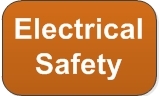 | Electrical safety |
- All electrical equipment and installations designed, constructed, installed, maintained, protected, and used to prevent danger
- Get a qualified electrical contractor to carry out installation and repairs to electrical equipment and fittings
- Maintain proper pest control to avoid rodent damage to electric wiring and equipment
- Check electrical equipment and remove defective equipment
- Ensure electrical cords are in good condition
- Plug appliances and lights into separate electrical outlets
- Avoid using extension cords. If you require an outlet in an area where there is none, have one installed by a qualified electrician.
- Use extension cords safety - not under carpets or across walking areas
- Use only one device per outlet
| 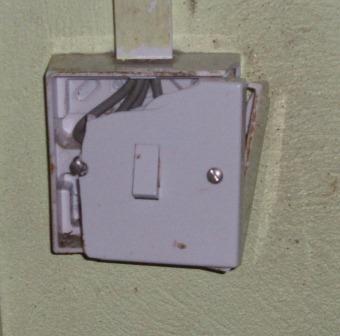 |
Back to top
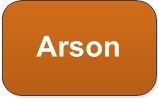 | Arson |
Deliberately started fires pose very significant risks to all types of workplace.
The possibility of arson should be considered as a component of your risk assessment and it is one that you can do much to control. The majority of deliberately started fires occur in areas with a known history of vandalism or fire-setting. Typically, local youths light the fires outside the premises as an act of vandalism, using materials found nearby. Appropriate security measures, including the protection of stored materials and the efficient and prompt removal of rubbish, can therefore do much to alleviate this particular problem.
You should therefore seek advice from the local Gardaí or the fire authority who will involve the other agencies as appropriate. Occasionally, arson attacks in the workplace are committed by employees or ex-employees. Employers and other workers should be aware of this potential threat and be alert for early signs, such as a series of unexplained small fires. Again, the Gardaí or the local fire authority can provide further useful guidance.
- Provide adequate security: exterior/interior lighting, intrusion alarms, guard service, well-secured access openings
- Prevent access by unauthorised personnel
- Keep flammables properly stored and secured
Back to top
Oxygen
Oxygen gas is used
- in welding, flame cutting and other similar processes
- for helping people with breathing difficulties
- in hyperbaric chambers as a medical treatment
- in decompression chambers
- for food preservation and packaging
- in steelworks and chemical plants
The air we breathe contains about 21% oxygen. Pure oxygen at high pressure, such as from a cylinder, can react violently with common materials such as oil and grease. Other materials may catch fire spontaneously. Nearly all materials including textiles, rubber and even metals will burn vigorously in oxygen.
With even a small increase in the oxygen level in the air to 24%, it becomes easier to start a fire, which will then burn hotter and more fiercely than in normal air. It may be almost impossible to put the fire out. A leaking valve or hose in a poorly ventilated room or confined space can quickly increase the oxygen concentration to a dangerous level.
The main causes of fires and explosions when using oxygen are
- oxygen enrichment from leaking equipment
- use of materials not compatible with oxygen
- use of oxygen in equipment not designed for oxygen service
- incorrect or careless operation of oxygen equipment
(Information from HSE UK - Take care with oxygen - Fire and explosion hazards in the use of oxygen - 8 pages)
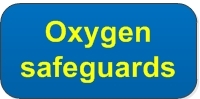 | Oxygen Safeguards |
- Ensure employees are aware of their responsibility to report dangers
- See safeguards in the Code of Practice for Working in Confined Spaces
- Oxygen should never be used to “sweeten” the air in a confined space
- Where oxygen is used,
- Be aware of the dangers of oxygen if in doubt, ask
- Prevent oxygen enrichment by ensuring that equipment is leak-tight and in good working order
- Check that ventilation is adequate
- Always use oxygen cylinders and equipment carefully and correctly
- Always open oxygen cylinder valves slowly
- Do not smoke where oxygen is being used
- Never use replacement parts which have not been specifically approved for oxygen service
- Never use oxygen equipment above the pressures certified by the manufacturer
- Never use oil or grease to lubricate oxygen equipment
- Never use oxygen in equipment which is not designed for oxygen service
- Operators of locations storing large amounts of oxidising substances have duties under the Control of Major Accident Hazards Involving Dangerous Substances Regulations (COMAH Regulations)
(Some information from HSE UK - Take care with oxygen - Fire and explosion hazards in the use of oxygen - 8 pages)
Back to top
Fuel
Workplaces in which large amounts of flammable materials are displayed, stored or used can present a greater hazard than those where the amount kept is small.
In relation to fire, fuel consists of flammable material. Flammable material is material that burns readily in a normal atmosphere. Flammable materials include flammable liquids (e.g. petrol), flammable gasses (e.g. propane and butane) and flammable solids (e.g. charcoal, paper). It is important to identify all flammable materials that are in your workplace so that proper controls can be put in place.
Great care is required in the storage, handling and use of flammable materials. Safety Data sheets may provide detailed advice.
Fuel Safeguards
Back to top
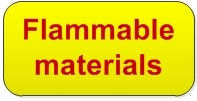 | Flammable materials |
- Identify all flammable materials so that proper controls can be put in place
- Identify use of substances with flammable vapours (e.g. some adhesives)
- Reduce quantities of flammable materials to the smallest amount necessary for running the business and keep away from escape routes
- Replace highly flammable materials with less flammable ones
- Store remaining stocks of highly flammable materials properly outside, in a separate building, or separated from the main workplace by fire-resisting construction
- Provide clearly marked separate storage for flammable chemicals, gas cylinders, and waste materials
- Train employees on safe storage, handling and use of flammable materials
- Keep stocks of office stationery and supplies and flammable cleaners' materials in separate cupboards or stores. They should be fire-resisting with a fire door if they open onto a corridor or stairway escape route
- Catering and hospitality premises – see relevant sections of Safe Hospitality, e.g. sections 1.13 LPG/ Gas Safety, 1.15 Fire Safety, 6.11 Flambé Lamps
- The US Occupational Safety and Health Administration has a webpage on combustible dust with tabs, beginning with information for users unfamiliar with combustible dust hazards
- See our information sheet on home heating oil (2 pages), and our information sheets on storage of hazardous chemicals in Warehouses and Drum Stores (4 pages) and Laboratories (4 pages)
Work on Gas Mains
See the press release "Construction firm fined €40,000 after workers sustain serious burn injuries" and the UK article “PPE saved worker from moreserious burn injuries”
Back to top
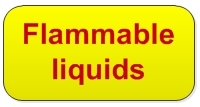 | Flammable liquids |
Flammable liquids can present a significant risk of fire. Vapours evolved are usually heavier than air and can travel long distances, so are more likely to reach a source of ignition. Liquid leaks and dangerous vapours can arise from faulty storage (bulk and containers), plant and process - design, installation, maintenance or use. Ignition of the vapours from flammable liquids remains a possibility until the concentration of the vapour in the air has reduced to a level which will not support combustion. | 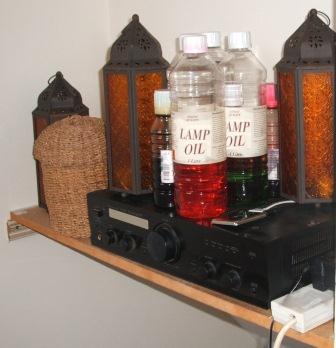 |
- The quantity of flammable liquids in workrooms should be kept to a minimum, normally no more than a half-day's or half a shifts supply
- Flammable liquids, including empty or part-used containers, should be stored safely. Small quantities (Tens of Litres) of flammable liquids can be stored in the workroom if in closed containers in a fire-resisting (e.g. metal), bin or cabinet fitted with means to contain any leaks
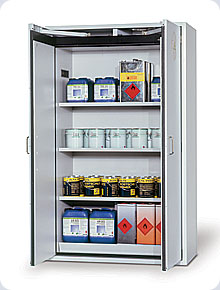 | Metal Storage for Flammable Chemicals to EN-14470-1 - Larger quantities should be stored in a properly designated store, either in the open air (on well ventilated, impervious ground, away from ignition sources) or in a suitably constructed storeroom
- Where large quantities of flammable liquids are used they should, where possible, be conveyed by piping them through a closed system. Where a connection in such a system is frequently uncoupled and remade, a sealed-end coupling device should be used
|
- Flammable liquids should not be decanted within the store. Decanting should take place in a well-ventilated area set aside for this purpose, with appropriate facilities to contain and clear up any spillage
- Container lids should always be replaced after use, and no container should ever be opened in such a way that it cannot be safely resealed
- Flammable liquids should be stored and handled in well ventilated conditions. Where necessary, additional properly designed exhaust ventilation should be provided to reduce the level of vapour concentration in the air
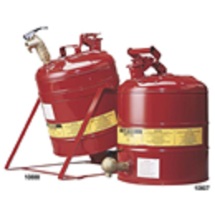 | Containers for Flammable Liquid - Storage containers should be kept covered and proprietary safety containers with self-closing lids should be used for dispensing and applying small quantities of flammable liquids
|
Intermediate Bulk Containers (IBCs)
The use of plastic and composite intermediate bulk containers (IBCs) for liquid storage has increased. They have a number of advantages over traditional steel drums, in particular; resistance to corrosion, efficient storage space use and ease of emptying when a valve is fitted. Plastic IBCs are used for hydrocarbons for: wastes; fuels such as diesel; solvents such as white spirit; lubricants; edible oils etc.
A number of serious fires in the UK started or spread because of the use plastic IBCs for combustible liquids. A characteristic of these fires was the rapid release of liquid from IBCs, inadequacy of bunding and damage caused as a result of the unconfined flow of burning liquid. This information is from HSE UK's advice on Intermediate Bulk Containers (IBCs) which includes a very helpful video. The Chemical Business Association and the Solvent Industry Association in consultation with the HSE UK have produced Guidance for the storage of liquids in intermediate bulk containers (22 pages) | 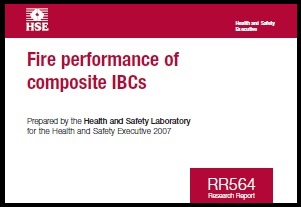 |
Plastic components of IBCs are easily ignited. Liquid loss from IBCs can be rapid and complete. In a fire, all of the liquid in unclad IBCs on level ground is likely to be released rapidly (in 5-10 minutes) and can produce large spreading pool fires. Ullage explosions can be extremely dangerous for anyone trying to fight the fire. Unless composite IBC design can reduce the rate of liquid drainage in fires, the potential of fires continues to be very serious.
- IBC users should be aware of the risks
- Risk assessments for IBC storage should be based on the premise that liquid loss will be rapid and complete
- Segregate IBCs and drums to avoid rapid catastrophic failure of drums and associated fireballs and projectiles
- Kerbs and partitions in storage areas may be useful in checking the flow of liquid and spread of fire
- For partitions to be effective, drainage must be carefully controlled
- All processes introducing a risk of ignition should be eliminated or tightly controlled
- Strict control of readily ignitable material is required
- IBC storage areas should be secure to deter casual vandalism
- Sites with large stocks of IBCs should consider drainage in the event of fire
- If there are sensitive targets nearby, substantial bunding may be required
- Manufacturers and re-conditioners should provide clear information on the potential behaviour of IBCs in fire
- Manufacturers should explore improvements in design
Back to top
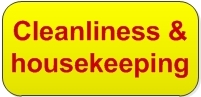 | Cleanliness and housekeeping |
- Avoid accumulations of combustible rubbish and waste and remove at least daily and store away from the building
- Never store flammable or combustible rubbish, even temporarily, in escape routes, or where it can contact potential sources of heat
- Position skips so that a fire will not put any structure at risk
- Clean cooking surfaces on a regular basis to prevent grease build-up
| 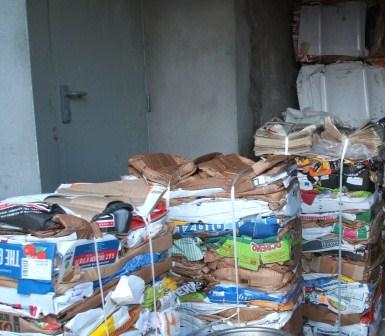 |
- In catering, clean ventilation ducts on a regular basis to prevent grease build-up
- Flammable or combustible rubbish should not be stored, even as a temporary measure, in escape routes such as corridors, stairways or lobbies, or where it can come into contact with potential sources of heat
- Parts of the workplace which are not normally occupied, such as basements, store rooms and any area where a fire could grow unnoticed, should be regularly inspected and cleared of non-essential flammable materials and substances. You should also protect such areas against entry by unauthorised people
- If the workplace has waste or derelict land nearby, you should keep any undergrowth under control so that a fire cannot spread through dry grass, for example
- There should be no potential ignition sources in areas where flammable liquids are used or stored and flammable concentrations of vapour may be present at any time. Any electrical equipment used in these areas, including fire alarm and emergency lighting systems, needs to be suitable for use in flammable atmospheres
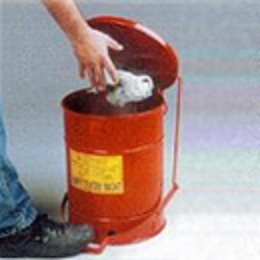 | Metal Container for Cloths Contaminated with Flammable Solvents - Rags and cloths which have been used to mop up or apply flammable liquids should be disposed of in metal containers with well-fitting lids and removed from the workplace at the end of each shift or working day
|
Back to top
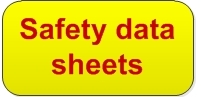 | Safety Data Sheets |
Safety data sheets provide useful information on chemicals and handling, storage and emergency measures. A safety data sheet should be provided with any hazardous chemical and includes useful information. Section 2 gives details on the hazards of the chemical and the potential effects and symptoms resulting from use. The information in this section must be consistent with the information on the label. Section 5 gives specific information on fighting a fire caused by the chemical, including the most suitable extinguishing media and protective equipment. Section 7 contains details on how to handle and store the chemical safely. Section 10 contains details of any hazardous reactions that may occur if the chemical is used under certain conditions. Section 14 contains information relating to the transportation of the chemical. Section 16 gives any other information relevant to the chemical e.g. training advice. | 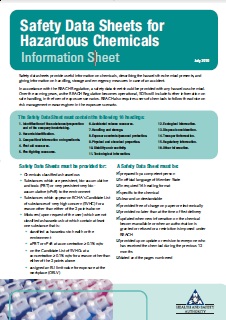 |
Back to top
Fire Prevention Diagram
This diagram gives an overview of fire prevention for workplaces
Back to top
Go to