Face Profiling and Drill Hole Logging
Any blasting incident resulting in injury, damage or even distress to neighbours can result in massive unwelcome costs to a Quarry operation and may even threaten its viability as a business entity. Some years on from its first use in the quarrying industry, there is now little doubt that laser profiling of free rock faces in quarrying operations has been a major step forward in the prevention of uncontrolled rock projections during primary blasting. Parallel to this, the incidence of remedial secondary blasting of toes has dramatically decreased. Borehole angle and alignment measurement systems have equally played a role and, indeed, added the final essential part of the control equation. In addition to the safety benefits of face profiling and borehole tracking the use of these techniques can markedly reduce the overall cost of the rock winning and processing operation. Armed with this information, The Explosives Supervisor and Shotfirer can precisely match the burden with the explosive charge, optimising blast ratios, not only for each hole but along the entire length of each hole. This results in significant reduction in drilling and blasting costs through increased efficiency. | 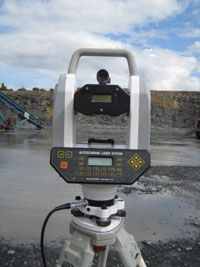 |
Face profiling requires the use of a laser scanner pointed at the face and measures the distance, horizontal and vertical angles directly across the rock face and accurately calculates the burden of the face along its length and height and this can be uploaded to a computer to produce a 3D image.
Borehole tracking data from down the hole tracking using a sensor head determines the inclination and direction of each borehole in relation to the face orientation at the surface and this information can be integrated directly into the 3D profile to give a complete picture of the face and drillholes along their entire length to allow for precise loading of each hole.
If the face profiling is carried out prior to the drilling the information can be used to accurately set out the burden and spacing of the drillholes and the borehole tracking can then be undertaken following the drilling and the precise information added to the profile to determine the blasting ratio of each drillhole.