Drilling of Shotholes
As regards safe blasting operations the drilling of the shotholes is probably the most important factor as it is the initial operation and inaccuracies and issues at this stage can cumulatively affect the blast.
Activities prior to commencing drilling operations
- Before drilling operations commence the driller should examine the extraction face from the bottom to look for geological problems, loose or shattered rock or dangerous overhangs, and areas of potentially reduced burden.
- At the top of the quarry face the driller should check for ground stability issues, excessive cracking of the rock, shear planes or other potential rock failures.
- If issues are identified then the Driller must raise these with the appropriate responsible person such as the Operator, Manager, Explosives Supervisor and Shotfirer and if necessary the blasting specification should be amended.
- The Driller should thoroughly check their equipment prior to tracking into position, these checks should include the condition of the drill string and the drill bit/hammer, the operation of the dust extraction equipment, guarding of moving parts and the condition of hydraulic hoses.
- The Driller should not commence any drilling operations unless adequate edge protection is in place at the quarry face. If the Driller is required to erect the edge protection then they must carry out such operations using suitably anchored fall arrest equipment. Edge protection should not be erected using drillholes that will require charging as part of the blast as there will be no fall protection available when charging the front row of holes.
- The Driller should not commence Drilling Operations unless they have been provided with a blasting specification or other information that specifies the required burden, the spacing of holes and subsequent rows, the number of holes and rows, the depth, azimuth* and vertical angle of the shotholes including any required sub-drilling.
| 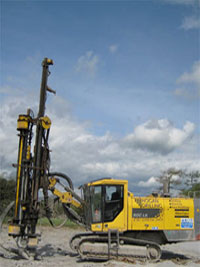 |
*The azimuth is the angle of the drill hole direction as projected to a horizontal plane taken along the quarry face and relative to due North. By industry convention, 0 degree azimuth coincides with North, 90 degree azimuth with East, 180 degree azimuth with South, and 270 degree azimuth with West. This is very important as the inclination of an inclined drill hole should normally be in the direction of the horizontal plane of the quarry face and subsequent drill holes should follow that direction to prevent diverenge or convergence.
Drilling Activities
The driller must take all possible steps to avoid deviation of drillholes as reduced burden or intersection of shotholes is a significant hazard that has a high potential for injury to persons and property damage. Good practice should minimise drillhole deviation to 2 or 3°.
The driller should accurately mark out the position and spacing of the drillholes. Poor marking out can result in an inadequate burden causing fly rock, air blast, high explosives and drilling costs, and poor crusher utilisation.
The drill bit should be in good condition and be of the correct diameter for the required drillhole a small increase in the required drillhole diameter can significantly increase the amount of explosives in the drillhole and lead to overcharging.
Eliminating collar position errors can be achieved by using painted lines and not moveable objects such as rocks. Measuring tapes, optical squares or alignment lasers can be used to ensure accurate collar positions. Completed shotholes should be protected by shothole plugs to prevent holes from caving in or filling up.
The Driller must ensure that each drillhole is drilled to the correct depth including the required sub-drilling, if the holes are intended to be inclined then the length of the drillhole must take into account the vertical distance required and the angle of inclination.
The Driller must correctly determine the azimuth and the direction of each drillhole so that it matches the proposed blast direction.
Good practice for quarry face control is to keep the maximum height of the extraction face to 15 metres and drill hole deflection issues can increase greatly above this height, drill hole deflection is also influenced by the type of bit used, the drilling technique employed (rotary drag bits or roller bits, percussive, pneumatic or hydraulic drilling using down the hole or top hammer), the torque applied to the drill string, the rock characteristics etc. Guide tubes can reduce drill string deflection and drill string bending can be reduced by using a lower feed force. If angled holes are used then account needs to be taken of the gravitational effects that can lead to drill string sagging.
It is not possible to predict the direction or magnitude of deviation of drillholes which is why the control measures above can minimise the amount of deviation.
Drillers Log
The Shotfirer and Explosives Supervisor rely heavily on the information provided by the driller. The drill log reveals the full history of the drilling operations and variations in the rock formations drilled. If some valuable information comes to the attention of the driller whilst the drilling is in progress the driller should record it in the log and ensure that it is brought to the attention of the shotfirer/explosives supervisor. The Driller should have the knowledge and experience to interpret if something unusual is happening in terms of drilling rates, excessive vibration, drillhole deviation, wall stability, chip size, shape and condition, evidence of water or other abnormality. A sample drillers log can be accessed here
Borehole tracking
Although it is possible to carry out a rough check of the direction and angle of a drillhole using an inclinometer and a torch, drillhole deviation errors can only be accurately determined using an effective borehole survey tool. Borehole tracking uses a measuring head attached to lightweight rods that are lowered down the hole and take measurement along various points in the hole. The results can be used in conjunction with face profiling equipment to accurately determine the burden and spacing of drillholes along their full length. There is more information on face profiling and borehole tracking here