Microbiological Safety Cabinets
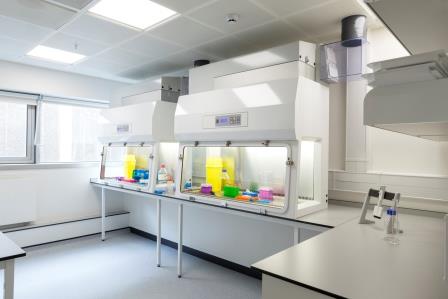
A microbiological safety cabinet (MSC), often referred to as a biological safety cabinet, a biosafety cabinet or a safety cabinet, is a form of local exhaust ventilation (LEV).
Examination, Maintenance and Testing
Depending on local circumstances, the MSC should be thoroughly checked at least every 14 months or more frequently if the manufacturer recommends it, in order to ensure it is performing to design. For low risk use such as in containment level 1 conditions, annual service and testing may be acceptable subject to risk assessment. For use with higher category agents such as risk group 3 agents, 6 monthly service and testing may be more appropriate. Simple routine checks should also be carried out when the system is in use e.g. by checking alarms, indicators, manometer readings are in the correct range, measuring face velocities, carrying out smoke tests etc.
A record (log book) should be kept which indicates the initial design criteria and required monitoring checks, the actual records and dates of performance monitoring, maintenance, parts replacement or any modification to the system. Maintenance records should be kept from year to year to demonstrate on-going effectiveness of the system and to assist in determining any deterioration by comparison of results. As maintenance may increase the potential for exposure to contaminants e.g. dirty filters and entry into confined spaces, where appropriate documented safe systems of work must be in place for decontamination and confined space entry.
Training
Personnel must receive appropriate training prior to using a biological safety cabinet. Training should cover the type of cabinet, how it provides protection and the limitations of its performance, how to use it correctly and work safely in it, the function of all controls and indicators, the appropriate and inappropriate use of the cabinet, the procedure for decontamination after use and the principles of airflow and operator protection tests. A documented procedure on the safe operation should be available to employees. Records of such training should be kept.
Fumigation
- A documented risk assessment should be available for cabinet fumigation.
- Documented safety control procedures such as a documented safe system of work and permit to work system should be in place for fumigation.
- The use of the fumigant should be risk assessed under the Safety, Health and Welfare at Work (Chemical Agents) Regulations 2001 to 2021.
- Appropriate warning signs, in line with Chapter 1 of Part 7 of the Safety, Health and Welfare at Work (General Application) Regulations 2007 to 2023 (commonly known as the Safety Signs at Places of Work Regulations), must be displayed and access to the area restricted.
- The fumigator must be trained in the use of the equipment and understand the hazards of the materials being used.
- The fumigator must be fit tested and trained in the use of the respirator.
- Each fumigation should be documented and recorded.